Making a knife doesn’t mean you have to start with a lawn
mower blade and a forge. A variety of
steels in terms of grade and types are available. Also available are knife kits which in which
the blade is pre-shaped and
sharpened. These kits also come in a variety
of completion. Some have all the
components and you assemble your knife. Other require a little more effort on
your part.
Woodcraft offers a variety of learning projects so I signed
up for the knife making. I wanted to see
how they handled epoxying and pinning handles.
As you’ve seen on Forged In Fire, pinning handles onto your knife is one
of the major stumbling blocks for contestants.
They need to drill through steel, align holes, hammer pin in place while
the five minute epoxy is hardening.
 |
Basic kit plus wood handles |
Here’s my kit and I’m using a light olive wood for the
handle. The first step is to turn a 3/8
inch thick slab into two slabs. The
second is to tape your blade with removable painters tape. Use lots of tape to protect your hands from
the edge. Safety first.
 |
Turning one piece of wood into two |
We traced the handle on the wood blanks making sure a square
end of the wood are in complete contact
with the bolster, then on to the band saw.
Removing excess wood is a time saver, but leave enough just in case your
handle needs to be finessed a little. But
really, a hand coping saw would have worked just as well. You could just sand it all away too.
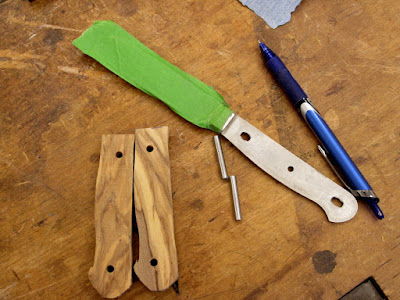 |
Taped, trimmed, ready for epoxy |
After you assure yourself each side of the knife’s handle
has the correct cutout, the pins fit correctly and you’re happy with everything,
dry fit it together again. Can’t be too careful!
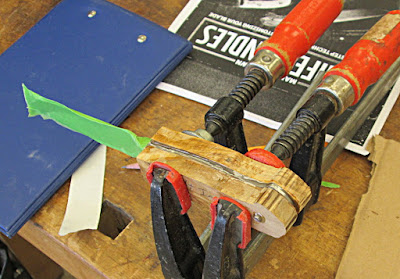 |
Clamped |
Now get the clamps out and mix your epoxy. So, Bunkie, five or thirty minute epoxy? The class used five minute because it is fast
and we gave it a half hour. I like the thirty
minute or longer. I want the longer time
for fixing an “Oops!” and I believe longer cure epoxy is stronger. While I have no plan to destroy an elk’s
skull or batter the hood of a 1948 Ford pick-up truck with my knife, stronger
always seems better to me.
After the epoxy is cured, it is sanding time. Woodcraft has a variety of terrific sanders,
rotary oscillators with different radius, belt sanders, disk sanders but all
you really need is any sander you have and patience.
 |
Sanding in process. |
Your plan of attack is different from anyone else. I like a rounded handle with a palm swell and
flat top. Start removing wood, but
remember the Golden Rule of carpentry:
It’s easy to take wood off, very hard to put wood back.
Keep handling your knife.
How does it feel to you? Too thick? Too rough?
Edges sticking up? Keep
working. And while you’re striving to
make your knife, remember perfection is the enemy of accomplishment. Experiment with it. Do you want an asymmetric “D” shape handle or
maybe oval facets?
 |
Finished |
When you get it to the shape you want, move to a finer grit
paper. Work your way down to a finish
you want. How about polishing to a 4000
grit finish? The wood starts to come
alive the more sanding dust you create.
The wood finally explodes to life with a finish. You can stain it, wax it, linseed oil it,
urethane it. That’s up to you. I used a coating of flax seed oil. Just a fancy name for linseed. That a drying oil, so I left it outside in
the sun to help cross link the finish.
 |
Just one variety of the steel and blade shapes available |
It’s not perfect, but the next one I make will be
better. I know what to look for and what
to watch for. And I know how much fun it
was.